Patented Advantages of a “Blade with Variable Thickness”
Wind Harvesters use extruded blades made from aircraft aluminum. The fiber and resin blades of most wind farm scale HAWTs (horizontal-axis wind turbines) use custom molds and a lot of skilled labor. Extruded blades are much less expensive to manufacture and if made like ours, have a fatigue life of over 70 years and are fully recyclable.
Our Model 3.1 blades needed reinforcing at the connections to the upper and lower level arms to help alleviate stress concentrations caused by the bolt holes. Here are some photos of Omar and Antonio adding a precisely crimped aluminum plate to where the holes are located, increasing the skin thickness and reducing the stress concentration at the area where the blade is connected to the arm. Sanding, acid etching, toxic epoxy, careful alignment and precise pressure, temperature and humidity were needed. After installing six of these plates, our engineers were motivated to find a way not to use them.
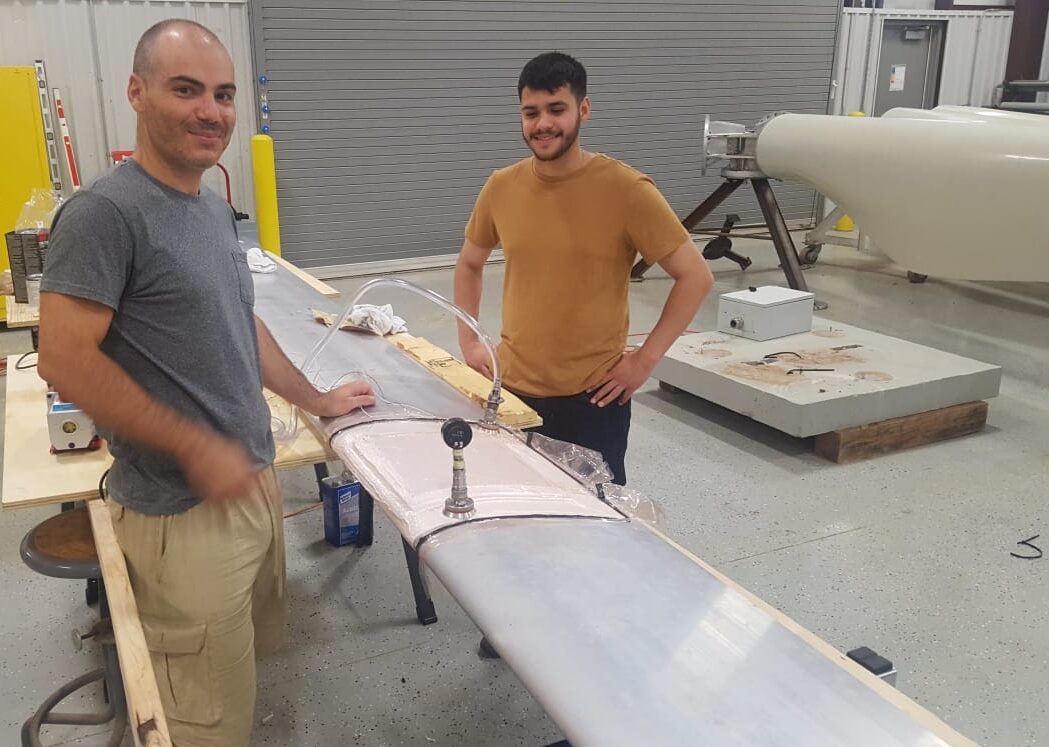
Antonio (left) and Omar (right) finish fixing the first plate to a blade and will wait for the epoxy to cure.
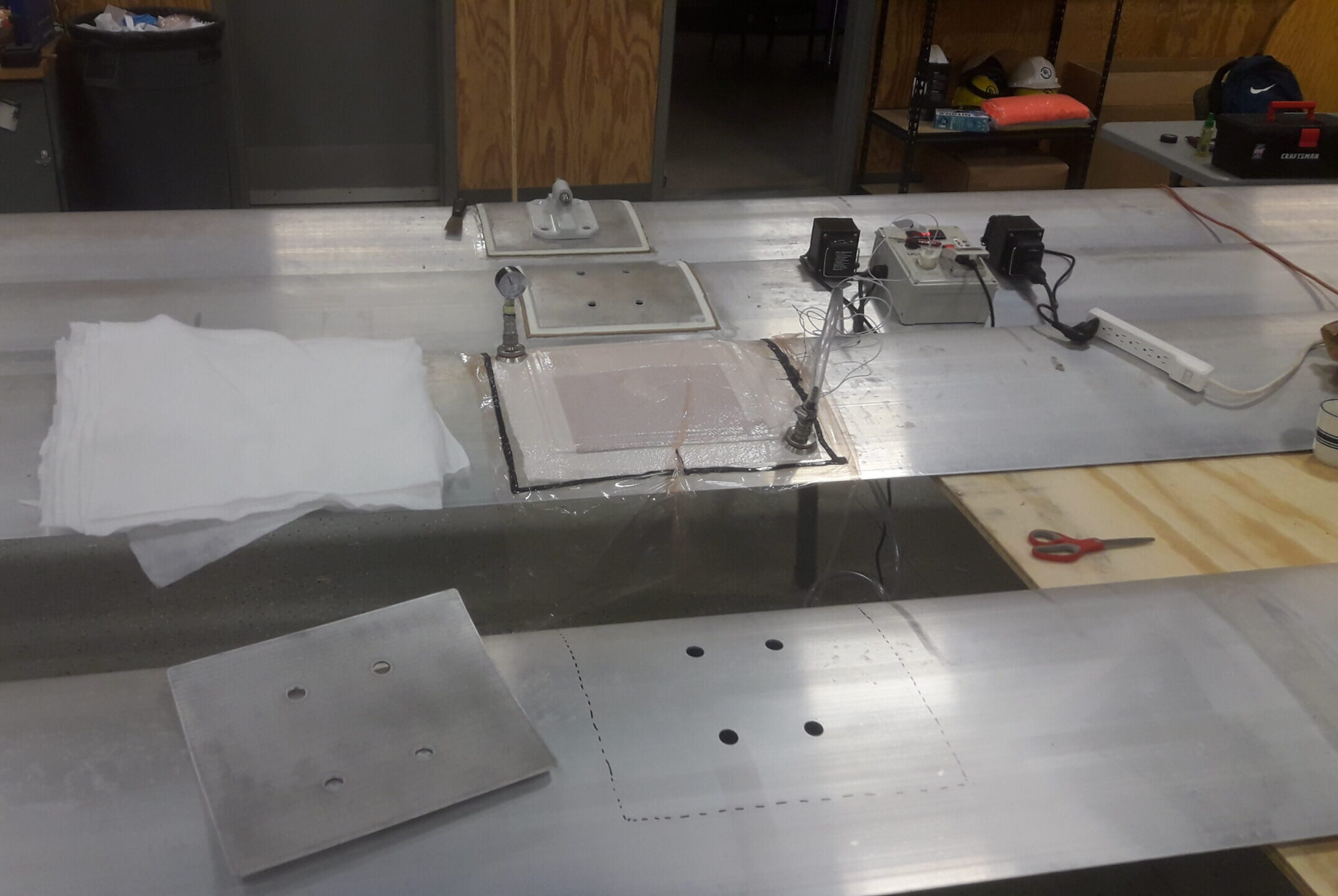
Three plates done. A fourth ready for sanding, acid etching and adding the epoxy.
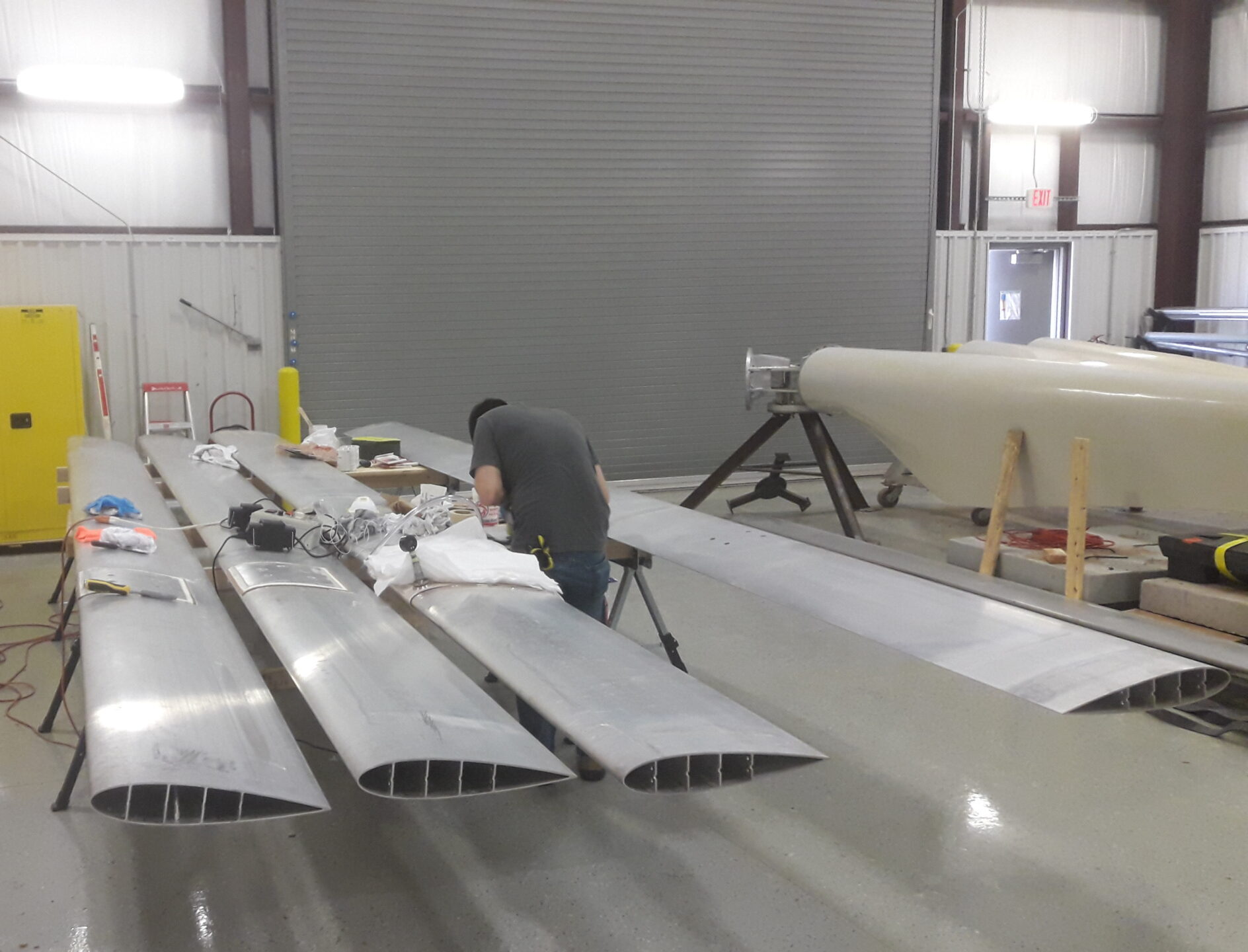
Note the end of Model 3.1 blades show the uniform width of its skin and interior walls.
So we hired Iopara Inc to evaluate three different shaped blades plus the NACA 0018 blade that we’d used on just about every turbine since co-founder Bob Thomas (deceased) started designing and testing vertical-axis wind turbines. Iopara’s aerodynamic modeling showed that an almost 50% larger, NACA 0021 shaped blade would produce about 3% more energy than any of the other profiles.
Nutbar showing the customized curve to match the blade and the threaded hole for the installation rod.
Now, how could we use this bigger blade and remove the need for the epoxied plates?
Our brilliant engineering team figured out that some parts of the blade could be thinner and others thicker without changing its weight or core strength. An extrusion die easily accommodates this variability. The bad news is that others have used variable thick blades, so that is not patentable. The good news is that no one can prevent us from using this.
Last week the US Patent and Trademark Office (USPTO) informed us that there was part of the variable thick blade idea that no one had thought of before – the internal nutbar bracket. These photos of the nutbars for Model 3.1 explains why this bracket will save money and assembly time.
You have to look closely to see that Model 3.1’s nutbar is custom made. The side that lies against the blade has to perfectly match the curve of the blade. Then on the edge, a threaded hole needs to be fabricated so that a rod can move the nutbar into position.
The nutbar holes line up with the blade arm bracket bolt holes.
Our “bracket” invention allows for an off-the-shelf nutbar to be used because the bottom of the bracket is extruded to be flat, not curved. The sides of the bracket guide the nutbar so that one can push it into position with a stick and the threaded rod isn’t needed. This invention saves hundreds of dollars per turbine in parts alone and even more in reduced labor costs.
The variable thick blade idea allows us to eliminate the epoxied plate and custom made nutbars. The increased loads the larger blade creates increases energy output. The icing on the cake is that this blade breakthrough triggered a slew of additional patents. We will share some of those in future blog posts. Stay tuned.
Nutbar with rod attached, ready to be moved into place five feet deep in the blade.
The connection bracket on the plate is bolted to the nutbar that is pushed five feet or so inside the blade to line up with its bolt holes.
Contact: Jen Hoover, jhoover@windharvest.com
Wind Harvest International, Inc. is a California-based renewable energy technology company, founded in 2006. The company makes, sells, and develops projects for its Wind Harvester brand of H-type turbines, the only known product designed to harvest the highly energetic, turbulent wind that blows 15-80 feet above the ground. Wind Harvest’s wholly-owned financial subsidiary Wind Harvest Pilot Project Inc. raises funds and loans it to the parent company.