Aerodynamic Drag on Model 3.1 Less than Predicted
Aerodynamic Drag on Model 3.1 Less than Predicted
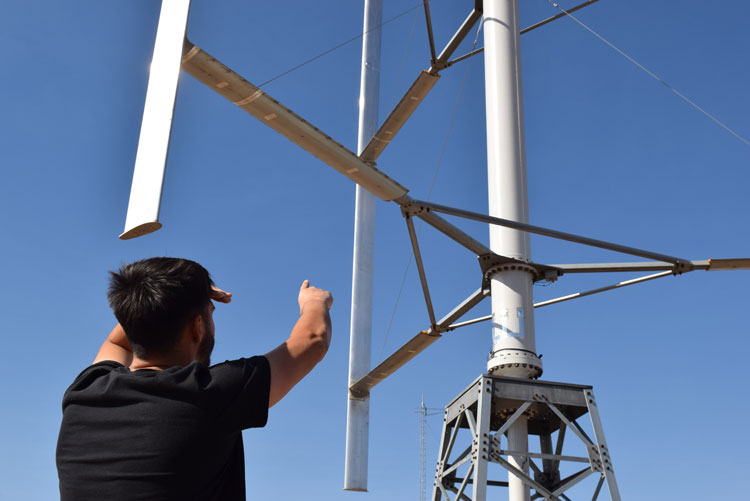
Omar Garcia, Soon to be Graduated mechanical engineer, and working full time with Wind Harvest, assists in the field portion of our model 3.1 drag test.
With the repair of the problematic caliper brake, the unanticipated errant mechanical drag has been eliminated. Thus, we were able to run new “true” operational tests that showed the Model 3.1 Wind Harvester energy production increased to more precisely match the predicted power performance curve produced from our original aerodynamic modeling.
Well, you probably wonder how we achieved this very important milestone!
On a near windless day, the team ran aerodynamic drag tests remotely by measuring the amount of power in kilowatts (kW) that was needed to motor the turbine at different rotational speeds (RPM) (30, 35, …60, 65). A physical paradigm involved in wind turbines and any other object moving against the wind is that drag on the object is proportional to the square of the wind speed, and the power required to overcome that drag is proportional to the cube of the wind speed. Thus, a doubling of wind speed results in a cubic increase in power needed to overcome the wind drag. Our test results were extremely satisfying. Measurements showed that it took 3 kW to motor the turbine at 30 RPM and 18 kW at 60 RPM, correlating with predictions. Yay. Our data is solid!
Another positive outcome from this drag testing deals with refining and improving our actual aerodynamic models. Dr. Malcolm’s analyses always incorporate conservative but realistic estimates of certain variables associated with his aerodynamic models until actual empirical data shows otherwise. His initial aerodynamic modeling used drag coefficients that turned out to be 17% higher than what the actual test data revealed. Of course, that doesn’t directly translate into a 17% increase in energy output because drag isn’t the only factor that affects power performance. But the results do indicate that we can expect increased energy output from our Model 4.0 than our modeling previously predicted.
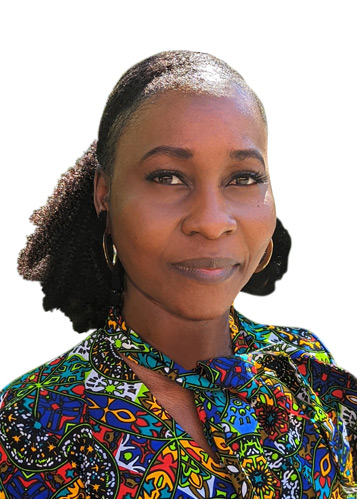
Dr. Ola Ajala
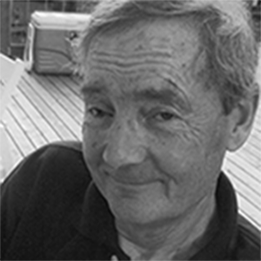
Dr. David Malcolm
Note that Dr. Malcolm and Dr. Ajala use this data to continually refine and improve our aerodynamic models. All in all, this was quite an excellent set of test results. These outcomes continually increase our confidence in the design and projected power output of our Wind Harvester turbines.
Test the waters disclaimer page here
Contact: Jen Hoover, jhoover@windharvest.com
Wind Harvest International, Inc. is a California-based renewable energy technology company, founded in 2006. The company makes, sells, and develops projects for its Wind Harvester brand of H-type turbines, the only known product designed to harvest the highly energetic, turbulent wind that blows 15-80 feet above the ground. Wind Harvest’s wholly-owned financial subsidiary Wind Harvest Pilot Project Inc. raises funds and loans it to the parent company.