Minor Maintenance, Major Savings with Wind Harvesters
Minor Maintenance, Major Savings with Wind Harvesters
07-22-2022
Model 3.1 has undergone some basic maintenance; we installed the automated grease cartridges for the bearings in the drive shaft and the generator. The process of maintaining Wind Harvesters is fast and simple, especially compared to the costly and time-consuming processes needed for maintenance on traditional turbines. See how we do it step-by-step below!
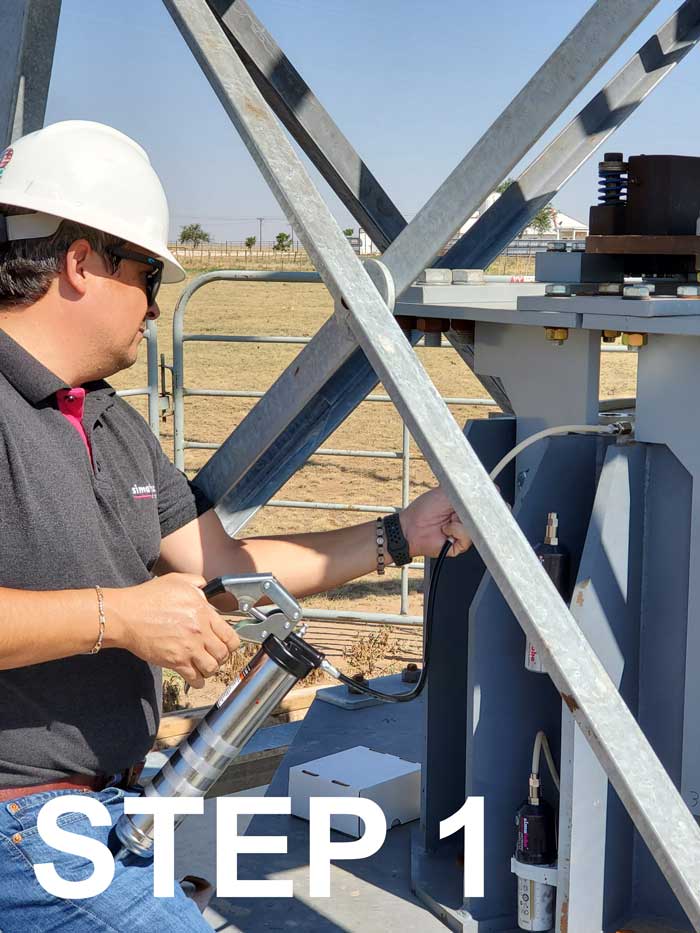
Step-1
Grease the Nipple.
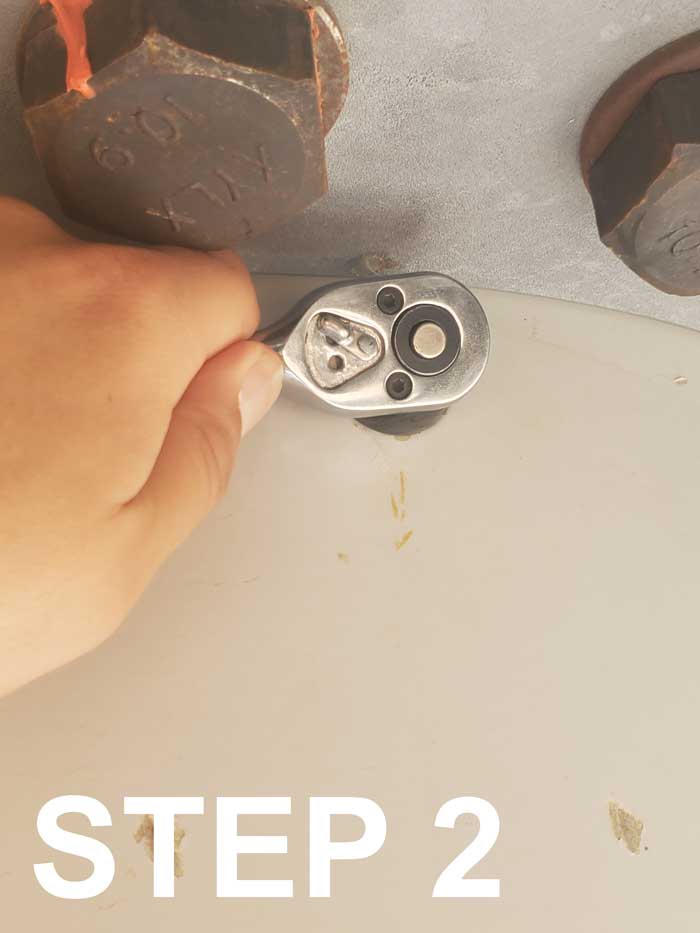
Step-2
Unnscrewed the nipple.
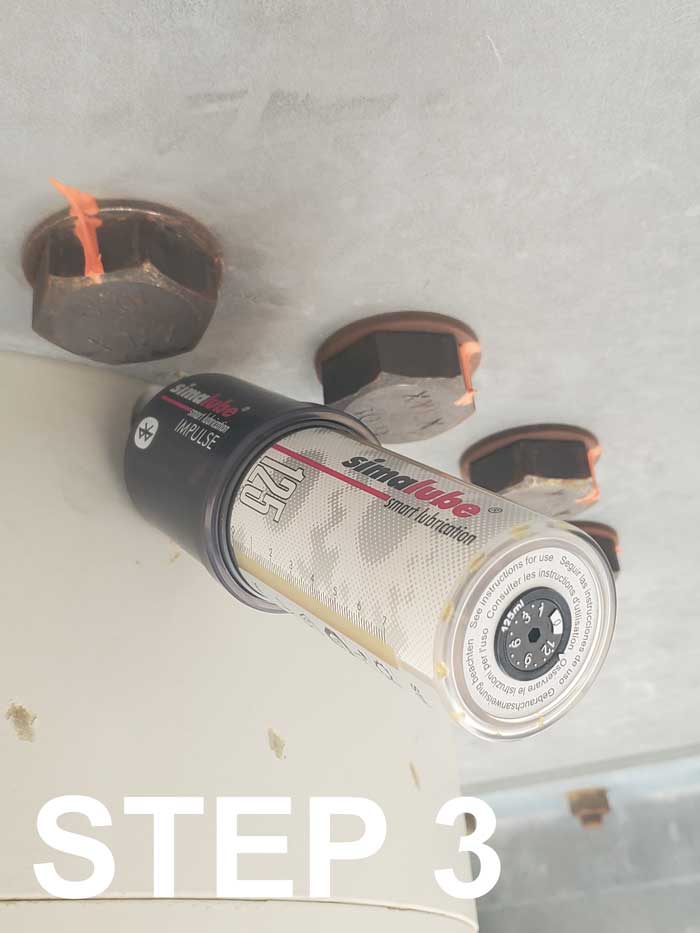
Step-3
Screw in the black Impulse device followed by the grease container.
Our turbines use slow-release canisters that gradually apply the lubricant over the life of the cartridge, essentially providing an ever-renewing supply and replacing what is lost during operation. These cartridges are relatively small; the turbine does not require very much lubricant. Of course, in the event something goes wrong or the bearing needs its lubrication replaced before anticipated, the cartridges are equipped with a Bluetooth-connected device that will alert our engineers. This is a good measure to ensure our equipment is always functioning safely.
Vertical-axis turbine blades rotate perpendicular to the ground, so they have no need to control the yaw (or indeed, no yaw to control), and they have a natural stall, so no pitch mechanism is necessary. Traditional turbines manipulate both to maintain maximum efficiency, prevent overspeeding, and assist in braking. Because HAWTs have these mechanisms in addition to the drive shaft and generator, they have more moving parts and require significantly more lubricant. Their gearboxes are not accessible at ground level, and their hub heights can exceed 300 ft—taller than the Statue of Liberty—so technicians must climb or be lifted high into the air to complete this maintenance. Many people would (rather reasonably) be reluctant to climb and work hundreds of feet in the air, but that is not a hurdle with the Wind Harvester turbines.
In a moderate-sized installation, the basic mechanical O&M for our turbines is projected to require approximately 4 man-hours per year to complete—substantive component replacements or modifications notwithstanding. Other than changing the lubricant, the O&M crew would check the hydraulic fluid in the braking system, perform torque confirmations, and make any necessary adjustments. Most of this can be completed annually, although in some locations, lubricants do need to be replaced every six months. Based on this maintenance schedule, we estimate a yearly O&M cost of about 0.3 cents per kWh, or around $3,300 per MW. If you compare this to traditional turbines, which have an average O&M cost of 1.5 cents per kWh or $15,000 per MW, then annually the cost of O&M on Wind Harvesters is only about 20% of the average HAWT!
This is true for comparing all aspects of O&M between the turbines. Because our Wind Harvesters have fewer moving parts and are significantly smaller, O&M is not only cheaper and less demanding, but it’s also significantly safer for the technicians and it requires much less training and specialization.
Test the waters disclaimer page here
Contact: Jen Hoover, jhoover@windharvest.com
Wind Harvest International, Inc. is a California-based renewable energy technology company, founded in 2006. The company makes, sells, and develops projects for its Wind Harvester brand of H-type turbines, the only known product designed to harvest the highly energetic, turbulent wind that blows 15-80 feet above the ground. Wind Harvest’s wholly-owned financial subsidiary Wind Harvest Pilot Project Inc. raises funds and loans it to the parent company.